Porosity in Welding: Identifying Common Issues and Implementing Best Practices for Prevention
Porosity in welding is a pervasive issue that frequently goes undetected till it triggers significant troubles with the integrity of welds. This typical problem can compromise the stamina and toughness of welded frameworks, posing safety and security threats and leading to costly rework. By recognizing the root creates of porosity and carrying out reliable prevention approaches, welders can dramatically boost the quality and integrity of their welds. In this discussion, we will certainly discover the key aspects contributing to porosity development, examine its harmful results on weld efficiency, and review the best methods that can be taken on to minimize porosity incident in welding procedures.
Typical Root Causes Of Porosity

Using dirty or wet filler materials can introduce pollutants into the weld, contributing to porosity problems. To alleviate these common causes of porosity, thorough cleaning of base metals, correct securing gas option, and adherence to ideal welding parameters are important practices in attaining high-quality, porosity-free welds.
Effect of Porosity on Weld High Quality

The existence of porosity in welding can considerably jeopardize the architectural honesty and mechanical residential properties of bonded joints. Porosity produces spaces within the weld steel, damaging its general strength and load-bearing capacity.
Among the main repercussions of porosity is a reduction in the weld's ductility and sturdiness. Welds with high porosity degrees often tend to display reduced influence toughness and reduced capacity to flaw plastically prior to fracturing. This can be especially concerning in applications where the bonded parts undergo dynamic or cyclic loading conditions. In addition, porosity can restrain the weld's ability to successfully transfer forces, causing early weld failure and potential security threats in essential structures.
Best Practices for Porosity Avoidance
To boost the structural integrity and high quality of welded joints, what details procedures can be carried out to minimize the event of porosity throughout the welding process? Using the correct welding method for the certain material being welded, such as adjusting the welding angle and gun setting, can further protect against porosity. Regular examination of welds and immediate removal of any problems visite site identified during the welding procedure are necessary practices to prevent porosity and create top notch welds.
Importance of Correct Welding Strategies
Carrying out correct welding techniques is paramount in making certain the architectural honesty and high quality of bonded joints, constructing upon the structure of my latest blog post effective porosity prevention actions. Too much warmth can lead to increased porosity due to the entrapment of gases in the weld swimming pool. In addition, using the ideal welding specifications, such as voltage, present, and travel speed, is important for accomplishing sound welds with minimal porosity.
Additionally, the option of welding procedure, whether it be MIG, TIG, or stick welding, must align with the specific demands of the project to make certain optimum results. Proper cleansing and prep work of the base metal, in addition to choosing the best filler material, are likewise necessary elements of skillful welding techniques. By sticking to these finest techniques, welders can lessen the risk of porosity formation and generate high-quality, structurally audio welds.
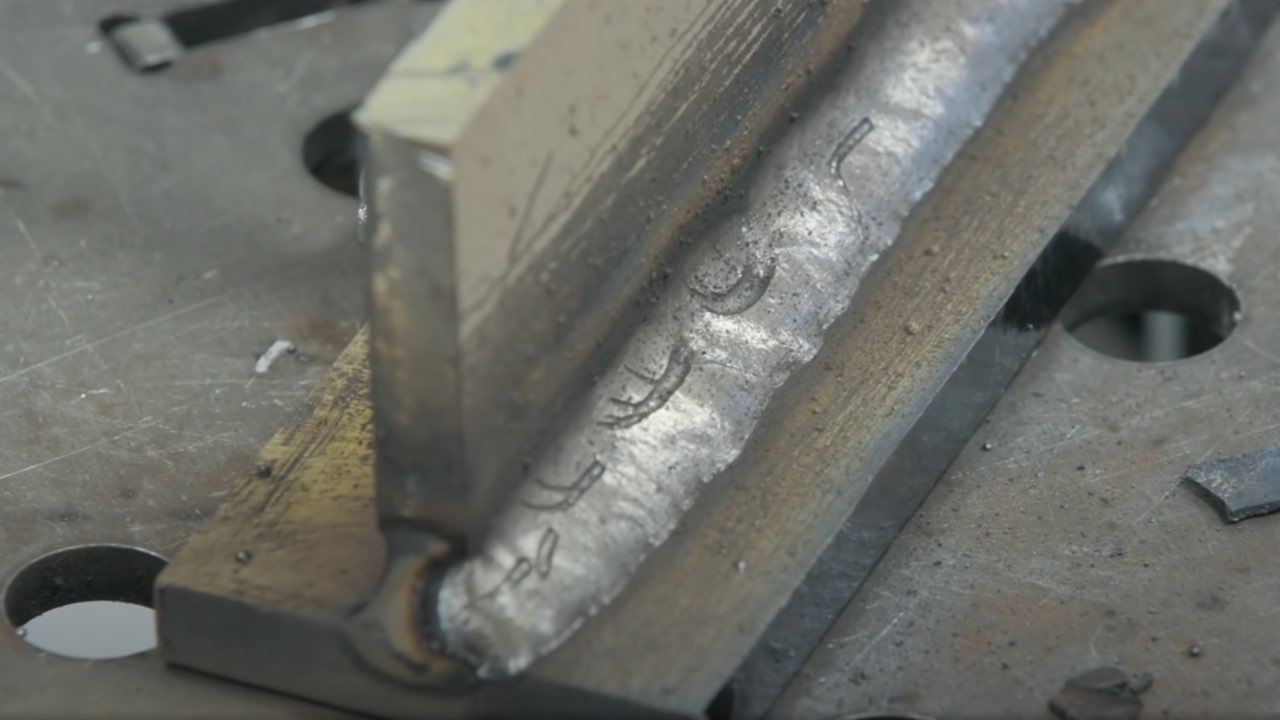
Examining and High Quality Control Actions
Quality control steps play a vital duty in verifying the integrity and dependability of welded joints. Examining treatments are important to spot and protect against porosity in welding, making certain the strength and longevity of the end product. Non-destructive screening methods such as ultrasonic testing, radiographic screening, and visual assessment are typically used to recognize possible problems like porosity. These strategies permit the assessment of weld quality without compromising the honesty of the joint. What is Porosity.
Performing pre-weld and post-weld examinations is likewise essential in preserving top quality control requirements. Pre-weld examinations involve confirming the materials, devices setups, and sanitation of pop over to this web-site the workplace to avoid contamination. Post-weld evaluations, on the various other hand, analyze the final weld for any kind of flaws, consisting of porosity, and confirm that it meets specified criteria. Implementing a thorough quality assurance strategy that consists of complete testing procedures and evaluations is paramount to lowering porosity issues and making sure the overall top quality of welded joints.
Verdict
To conclude, porosity in welding can be a common issue that influences the top quality of welds. By determining the usual reasons for porosity and executing best methods for prevention, such as proper welding strategies and testing measures, welders can guarantee top quality and trusted welds. It is important to focus on prevention methods to lessen the incident of porosity and keep the honesty of bonded structures.